3d Printing Phoenix is constructing a three-dimensional object from a CAD model. Various methods can be used to achieve this process.
Unlike traditional manufacturing methods, smarter 3D printers incorporate closed-loop learnings into fabrication processes to avoid untimely hold-ups and failures. This slashes part or product lead times by allowing them to be printed on demand and delivered to the point of need.
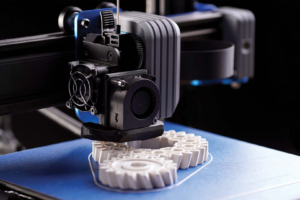
Additive manufacturing (AM) transforms digital CAD files into three-dimensional physical solid objects by depositing material layer-by-layer in precise geometric shapes. This approach allows engineers to design their products more flexiblely without worrying about production constraints or modifying existing designs to comply with traditional manufacturing processes. AM also reduces manufacturing costs and lead times, as well as the need for storing or warehousing parts.
The 3D printing process uses a variety of materials, including plastics, metals, and ceramics. It is a great way to fabricate prototypes and is ideally suited for mass customization. It can also be used to produce end-use parts for industrial applications. This technology can help manufacturers reduce their environmental impact, increase efficiency, and improve profitability.
Some of the most popular additive fabrication methods include stereolithography (SLA), selective laser sintering, and fused deposition modeling. These technologies use a printhead, nozzle, or other device to lay down material in layers and build the structure of the product. In addition to being highly accurate, these techniques also offer a wide range of material choices and are relatively affordable.
Another type of additive manufacturing is extrusion-based printing, which uses an extruder to melt and shape material to create a solid object. The process can be used to create complex structures with internal architecture, and the geometry of these structures is limited only by the CAD design capability. In addition, the ability to build multi-material components allows designers to optimize the performance of a final part by using different materials in specific areas.
While additive manufacturing is not new, there are ongoing advances in the technology. These advances include 4D and 5D printing, which enable printed objects to change shape over time. In addition, these machines can also be programmed to make multiple copies of a product at the same time, which saves a great deal of money.
Another exciting development in additive manufacturing is the potential to create custom-made spare and replacement parts for industrial equipment. This can be done on demand and reduces the need for storing or warehousing the parts, which can save organizations a lot of money in the long run. For example, some UltiMaker customers operate a “take one, make one” policy where they have spare parts printed on-site.
Material jetting
Whether you’re an automaker, design studio or medical organisation, material jetting is a valuable tool for creating reliable prototypes. It’s a printing technique that uses multiple colours and materials, and it’s one of the fastest ways to test new designs and products. It also provides exceptional detail. However, it’s not without its limitations. For example, it can be expensive and may not have the same strength and durability as parts made using other 3D printing methods. Furthermore, it’s not the best choice for parts that need to be able to withstand a lot of stress.
A material jetting printer works by jetting droplets of build material onto a build platform, and then curing them using UV light or heat. This process is similar to inkjet printing, and it’s the most common type of additive manufacturing. It’s also a popular option for producing full-colour and multi-material objects. The print head on a material jetting printer has multiple nozzles, and each nozzle can deposit different materials or colours. This allows the print to achieve a wide range of properties, including rigidity, flexibility, opaqueness and transparency.
The material jetting printing process can create complex shapes that wouldn’t be possible with other methods. It’s also relatively cheap and quick, which makes it an ideal choice for small-volume production of injection moulds or investment casting patterns. The precision of the material jetting process can help to produce highly accurate models with a smooth surface finish.
Material jetting offers many advantages over other printing techniques, but it’s not without its drawbacks. For example, the materials used can be expensive, and the prints may not have the same strength and durability as those created using other methods. In addition, the printed object can require a lot of post-processing to remove support structures and achieve a desired finish.
Material jetting is a great choice for making non-functional prototypes, but it’s not the best solution for functional products. The mechanical properties of the photopolymers used in MJ are poor, and they degrade quickly. Moreover, MJ machines are quite expensive, and they’re not suitable for high-volume production of parts. However, other types of additive manufacturing technologies such as vat photopolymerization and binder jetting can create parts with more reliable mechanical properties.
Sculpting
As 3D printing continues to expand, many sculptors are utilizing digital tools to create sculptures. The combination of digital sculpting and 3D printing is becoming a leading trend in the field of art. This digital process provides artists with greater flexibility and freedom, allowing them to fully express their artistic concepts and creativity.
When it comes to sculpting, the most important step is to observe objects in detail and envision the final product at first. This will help you get an idea of the overall shape of the sculpture and save you time. It is also helpful to have a reference photo or sketch on hand. Then, use sculpture techniques to create small drafts. Generally, multiple different drafts will be created to compare and choose the best one. Eventually, the draft will be enlarged to a larger size and shaped to form the final sculpture.
In addition to creating a digital model, sculptors also need to use post-processing techniques to polish the finished piece. This includes sanding, painting, and applying coatings to improve the final appearance and durability of the sculpture. These techniques are essential for 3D modeling and sculpting, as they can transform a raw printed object into a polished final product that meets specific artistic or functional standards.
Compared to traditional replication methods, 3D sculpting is much faster and more flexible. Moreover, it allows artists to experiment with various materials and colors, which are important for creating life-like sculptures. It can even be used to create complex designs and functional art objects. This technology has great potential to revolutionize the sculpture industry.
While traditional modeling is based on geometry and exact calculations, 3D sculpting is more creative and less prone to errors. It also gives the artist more control over the final results, allowing them to create more dynamic, realistic shapes.
Unlike conventional clay or wood, digital sculpting is easy to preserve. Once the sculptor finishes a work, they can quickly perform 3D scanning to obtain a digital backup of their work. This can be directly replicated with 3D printing, allowing the artist to easily restore their work if it is damaged or lost. This is a huge advantage over traditional methods, which may not provide a way to preserve works made of delicate materials.
Fabrication
In a 3D printer, an object is built layer-by-layer, similar to the way an inkjet printer prints. The nozzle dispenses a thin layer of plastic-like or waxy material, and waits until it hardens before adding the next layer. This process repeats until the object is complete. It can be used with a variety of materials, including plastic, wax, metals, and even ceramics. Once the print is finished, it may need rinsing in isopropyl alcohol or post-curing to stabilize mechanical properties. It can also need manual work to remove support structures or be cleaned with compressed air or a media blaster.
3D printing allows designers to quickly create prototypes of new products, saving time and money. It can be especially useful for companies that need to make complex parts that would be difficult or impossible to manufacture using traditional methods. It can also be used to create tooling, such as jigs and fixtures, which can help prevent costly production delays caused by missing tools or a lack of replacements.
CAD software can produce the models needed for 3D printing in a wide variety of formats. These files are typically called STL or OBJ. The majority of 3D printers can accept these formats, and many are compatible with several popular CAD programs. These include commercial packages like AutoCAD and free or open-source products such as Google SketchUp and Blender.
Some 3D printers use a multi-jet modeling system to build objects, which is one of the fastest methods. Other systems employ an ultraviolet laser to craft objects in layers. Some 3D printing systems use liquid resin to print with plastic, while others fuse small particles of powder together at high temperatures. The resulting parts can be sanded, buffed, or polished to improve their appearance and durability. Other printing processes, such as laser-sintering, selective laser melting, and stereolithography, are slower but produce superior results.